迪思科(DISCO)開(kāi)發(fā)出了利用激光從SiC鑄錠上切割SiC晶圓的新工藝“KABRA”。與使用線鋸的傳統(tǒng)方法相比,生產(chǎn)SiC晶圓的加工時(shí)間大約可以縮短到1/4,產(chǎn)量大約可以增加到1.5倍。部分客戶(hù)已經(jīng)開(kāi)始試用這次的加工方法。
目前從SiC鑄錠上切割SiC晶圓主要使用金剛石線鋸。但這種加工方法存在兩大課題。1個(gè)是SiC非常堅(jiān)硬,加工時(shí)間長(zhǎng)。另1個(gè)是線鋸切割部分的材料損耗大,會(huì)減少1只鑄錠可以切割出的晶圓數(shù)量。這些因素導(dǎo)致了SiC晶圓的生產(chǎn)效率降低,成本居高不下。因而抬高了SiC功率元件的成本。
利用激光設(shè)置分離層
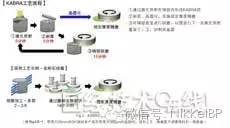
這次的加工方法與傳統(tǒng)方法
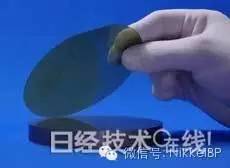
剝離出的口徑為4英寸的晶圓
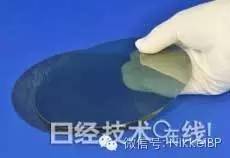
剝離出的口徑為6英寸的晶圓
這次的加工方法遵循以下步驟。首先,沿垂直方向,從SiC鑄錠的上面連續(xù)照射激光。通過(guò)這樣的方式,設(shè)置吸收光的“分離層”。這時(shí)可以以任意深度,形成扁平狀(激光入射方向與垂直方向)的分離層。接下來(lái)以分離層為起點(diǎn),剝離SiC晶圓的薄層。然后將剝離下來(lái)的晶圓研磨成需要的厚度并出貨(“規(guī)定厚度精磨”)。剝離后的鑄錠表面需要另行拋光,以準(zhǔn)備下一次的激光照射。通過(guò)重復(fù)這一連串的操作,利用1只鑄錠制作出一片片晶圓。
這種方法與使用線鋸的以往方法相比,縮短了加工時(shí)間,減少了裁切時(shí)的材料損耗。比如說(shuō),當(dāng)使用口徑為100mm(4英寸)、厚度為20mm的SiC鑄錠,生產(chǎn)厚度為350μm的晶圓時(shí),使用這次的加工方法切割出1片晶圓需要25分鐘,加工1只鑄錠總耗時(shí)約為18個(gè)小時(shí)。
而使用過(guò)去的方法加工1片晶圓大約需要2個(gè)小時(shí)(1.6~2.4小時(shí)),總耗時(shí)為2.5~3.5天。使用口徑為150mm(6英寸)的SiC鑄錠切割晶圓,使用這次的方法大約需要30分鐘,而過(guò)去的方法需要3個(gè)多小時(shí)。
材料損耗也較少
不僅縮短了加工時(shí)間,而且無(wú)需使用線鋸加工所需的“磨削”。在線鋸加工時(shí),晶圓表面會(huì)產(chǎn)生50μm左右的起伏。磨削的作用是去除這些起伏。這次的方法可以抑制起伏,省去了磨削的麻煩。
迪思科表示,使用傳統(tǒng)方法時(shí),每加工1片晶圓,線鋸切割部分的材料損耗約為200μm。而這次的方法是以分離層為起點(diǎn)剝離晶圓,幾乎沒(méi)有材料損耗。剝離后雖然需要去除分離層,但損耗可以控制在100μm。因此,1只鑄錠可以加工出的晶圓數(shù)量大約是過(guò)去的1.5倍。(記者:根津禎)
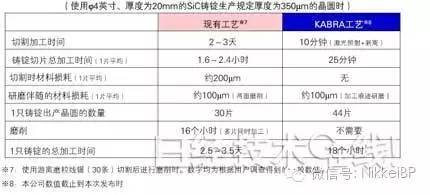
這次的加工方法與傳統(tǒng)方法的比較